A roller granulator specially designed for fertilizer manufacturing process. The fertilizer granulator machine is our main compound fertilizer granulating equipment, which has a wide market in domestic and international markets.
Roller extrusion granulator is a dry granulation process which uses pressure to agglomerate solid materials. Material is extruded by two reverse rotating rollers, which are driven by eccentric sleeve or hydraulic system. When the solid material is extruded, the air between the powder particles is first removed and the particles are rearranged to eliminate the voids between the materials. When brittle materials are extruded, some particles are crushed and fine powder fills the voids between particles. In this case, if the newly formed free chemical bonds on the surface can not be saturated by atoms or molecules from the surrounding atmosphere quickly, the newly formed surfaces will contact each other and form strong recombination bonds. When the plastic material is squeezed, the particles will deform or flow, creating a strong van der Waals attraction. At the stage of the extrusion process, the energy formed by the pressure to the system forms a hot spot at the point of contact between the particles, causing the material to melt, the temperature to drop, and the material to cool to form a fixed bridge. The large piece produced by extrusion is 5-20 mm thick, and the surface density is 1.5-3 times of the feed. The large sheet is flaked, crushed and screened to obtain the required particles.
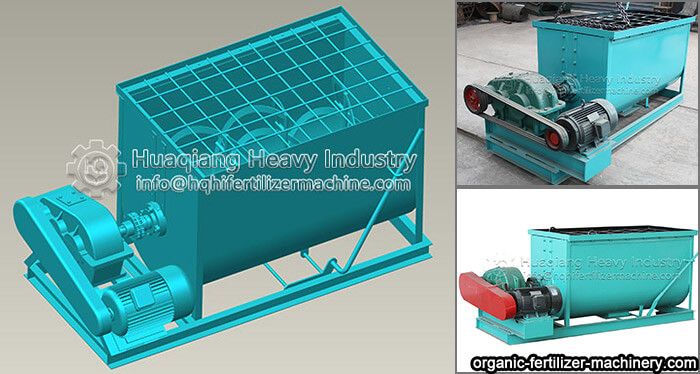
1. Roller clearance adjustment
First, loosen the bolt on the bearing seat, rotate the eccentric sleeve and adjust it to the required thickness so that the eccentric sleeve exerts a radial force on the driven shaft. When adjusting the gap between the two rollers, the two rollers can not collide. The minimum should be kept between 0.4 and 0.6 mm. Then tighten the bolt on the bearing seat.
2. Corresponding adjustment of ball socket
First loosen the bolt on the bearing seat, such as the axial misalignment of the ball socket, adjust the two eccentric sleeve cover bolt, so that the shaft moves left and right to adjust the ball socket relative. Tighten the bolts on the bearing seat. If the ball socket is not right up and down, first loosen the bolt of the debugging plate, then adjust the top wire of the concave part of the debugging plate, so that the counter shaft can be slightly turned to the ball socket. Then tighten the bolt of the debugging disc and loosen the top wire to use.