Control the drying temperature of sludge in fertilizer manufacturing process. Temperature is too high: the loss of organic matter is large; the cooling time is long, affecting the output, and the temperature of the material can not be lowered in a short time, and the sludge burning phenomenon is likely to occur when placed after packaging.
Strictly control the amount of feed in the fertilizer manufacturing process. According to the drying capacity of the equipment, the amount of feed is controlled to make the finished product meet the requirements. For the production equipment used in different processes, the corresponding production capacity of the machine is used for feeding.
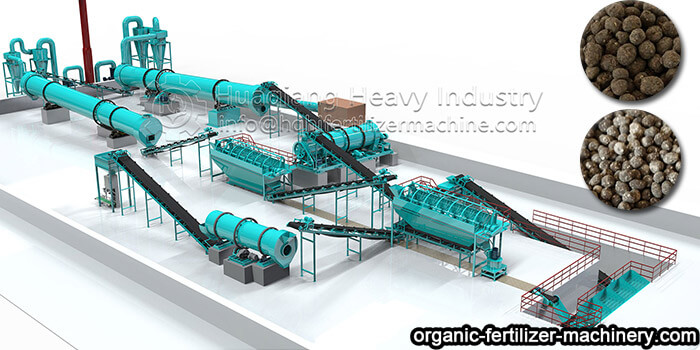
Control the mixing time and the amount of water added in the mixing process. Generally, stirring for 5 minutes is enough to make the material mix evenly. At the same time, the material can absorb a certain amount of water, which is conducive to granulation. Adding water in the mixing process is one of the characteristics of sludge fertilizer production process which is different from other compound fertilizer granulation process. First, sludge absorbs water slowly, which affects the granulation speed by adding water into the granulator machine; secondly, sludge dryer is lighter after crushing, which easily produces larger dust in the mixing and transportation process, and suspends in the air. Floating is not easy to sink, resulting in worse working environment. The method adopted is to add about 15% water in the mixing process. The method has been proved to be more effective, improve the working environment, and make the production process more smoothly.
Control the amount of water added in the granulation process. Because a part of water has been added in the mixing process, the spraying quantity must be controlled well in the process of fertilizer granulator machine. If the water spray is too large, it will easily produce a large ball. At the same time, the drying load will increase and the output will decrease. The water spray volume is small, the ball formation rate is low, and the defective products are increased. Since the sludge organic-inorganic compound fertilizer has less secondary granulation during the drying process, the spheroidization rate must be controlled above 80% during granulation; at the same time, the residence time should not be too long to prevent urea in the granulator dissolved inside to form large balls and sticky walls.
Strict control of drying temperature. Generally, the inlet temperature of fertilizer rotary drum dryer is 400-500℃, and the outlet material temperature is not more than 70℃. Low temperature, low drying efficiency and excessive moisture content of finished products; high temperature, which affects the quality of finished products, wastes raw materials (mainly urea) and energy.
Controlling the feed-back ratio of fertilizer manufacturing process. The experience of this fertilizer production line is that it is easier to return no more than 25% than that summarized by production practice in recent years.